From the center, move outward alternating both directions in 10 lb steps.
Randy, found this from a Cobra forum.
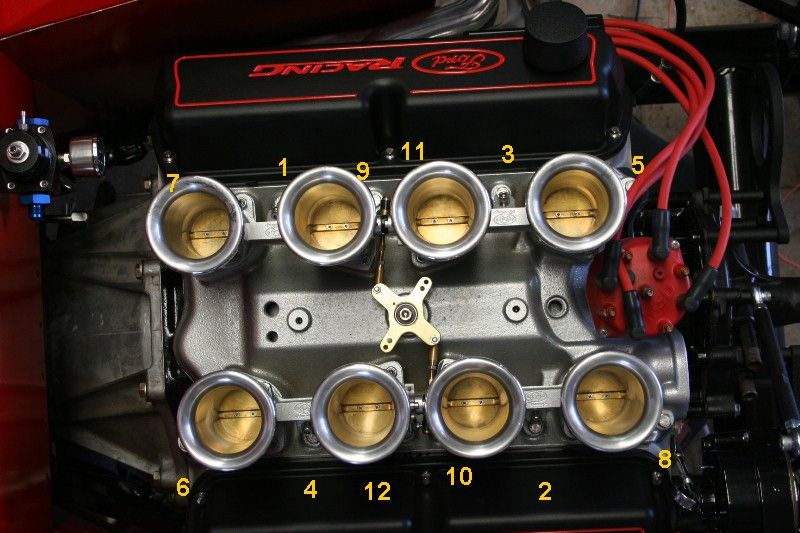
From the center, move outward alternating both directions in 10 lb steps.
Duke......
Here is something to ask Santa for this Christmas
Randy, found this from a Cobra forum.
![]()
Is that to tighten down the heads or the manifold?
How many fixings has each cylinder head got?
Randy is right, the definitive answer will come from the head manufacturer but the sequence I'm used to is....
9 5 2 4 8
7 3 1 6 10
Guys....guys....guys!
We are talking about the intake manifold, not the heads.
.....it's not like a fussy stroker motor......
DYou might want to check out the Weiand website technical info section for your model intake just to confirm what they recommend for it.
Gene
Having the heads cleaned and surfaced. Please share your torque procedure.
Was there warpage on the heads?
How much did the machine shop mill off the heads?